|
|
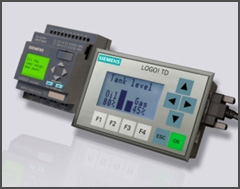 |
The consistently modular design of LOGO! makes it extremely flexible. A wide range of modules allows individual expansion of LOGO! to 24 digital inputs, 16 digital outputs, 8 analog inputs and 2 analog outputs! Communications modules are also available for AS-Interface and KNX (Instabus network for building automation). Now it is also possible to use the analog output module to solve simple closed-loop control tasks. Heating and cooling systems can be designed with the RTD PT100 module using special functions for PI control, ramp response and analog multiplexing. |
|
 |
Different voltages, i. e. 12 V DC, 24 V AC / DC, 115 / 240 V AC / DC – Can be used for a wide range of applications |
 |
Automatic changeover for configured daylight saving time – Reduces maintenance overhead |
 |
Password protection – Protects your engineering IP |
 |
38 integrated, pre-tested functions – No additional devices, such as elapsed time counter, are required |
 |
Linking of 200 functions is possible – Extensive applications can be implemented without restrictions |
 |
Eight digital inputs (incl. four AIs at 12 / 24 V DC) and four digital outputs on board |
 |
Flexibly expandable up to 24 DIs, 16 DOs, 8 AIs and 2 AOs – Protects original investment – Suitable for a wide variety of applications |
 |
Display of message texts, action items and current values as well as direct modification of the values on the display (except for Pure versions) |
 |
Retentive data memory – Protects current values against loss in the event of a power failure |
 |
Software LOGO! Soft Comfort V6 for user- friendly generation of control programs on PC; suitable for a variety of operating systems, such as Windows 95/98, NT 4.0, Me, 2000, XP, Vista, MAC OS X 10.4 with J2SE 1.5.0 and SUSE LINUX 10.0. |
 |
Connection facility for remote text display on all 0BA6 base modules |
|
|
The technology power supply for demanding solutions |
 |
Controllable backlight and multi-language |
Character sets |
 |
Supports 12 or 16 standard characters per line |
 |
Display of up to 50 messages on the LCD and/or the external TD |
 |
Switch between 2 screens or scroll up to 32 characters on any or all lines for each message |
 |
Display of up to 4 bar graphs and 4 I/O statuses per message/per character set |
 |
Password protection of RUN/STOP options on the TD |
|
 |
|
|
 |
The Micro PLC SIMATIC S7-200 is truly in a class of its own: it’s both compact and highly powerful – especially considering its real-time response – it’s fast, features great communication options and comes with easy-to-operate software and hardware. But there’s more; the Micro PLC SIMATIC S7-200 has a compact modular design – for customized solutions which aren’t too large, but flexible enough to be expanded anytime in the future. |
All this makes the SIMATIC S7-200 a great choice for open-loop control in the lower performance range. Become one of the thousands of S7-200 customers that constantly benefit from Siemens PLC innovation and lower cost of ownership.SIMATIC S7-200 delivers consistently economical solutions. The entire system family features |
 |
powerful performance |
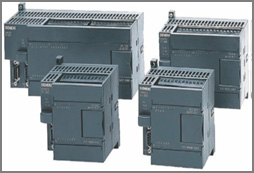 |
 |
optimum modularity |
 |
optimum modularity |
In addition, the SIMATIC S7-200 programming tools make your job even easier: this Micro PLC is easy to program allowing fast and easy realization of applications – and the add-on software libraries accelerate special function configuration even more. |
|
This Micro PLC has been in successful use in millions of applications around the world – in both stand-alone and networked solutions. |
Open communication |
 |
Built-in RS 485 interface with data transmission rates up to 187.5 kbit/s |
 |
PPI protocol system bus for trouble-free networking |
 |
Freeport mode programmable for userspecific protocols for any peripheral devices |
 |
Fast connection to PROFIBUS using the slave module |
 |
Powerful connection to AS-Interface using the master module |
 |
Communications anywhere using the modem module (for remote maintenance, teleservice or telecontrol) |
 |
Connection to Industrial Ethernet via the Ethernet module |
 |
Internet connectivity, e-mail, HTTP, and FTP server functionality using the Internet module |
 |
S7-200 PC Access – OPC Server for simple connection to the PC environment |
|
Powerful performance |
 |
Small and compact – ideal for any applications where space is tight |
 |
Basic and advanced functionality in all CPU models |
 |
Large program and data memory |
 |
Outstanding real-time response – being in total command of the entire process at any time means increased quality, efficiency and safety |
 |
Easy-to-use STEP 7-Micro/WIN engineering software – ideal for both beginners and experts |
|
Optimal modularity |
 |
Systems engineering: |
 |
5 distinct CPUs in the performance range with comprehensive basic functionality and integrated Freeport communications interface |
 |
A wide range of expansion modules for various functions: |
|
 |
Digital/analog expansions, scalable to specific requirements |
|
 |
PROFIBUS communication as a slave |
|
 |
AS-Interface communication as a master |
|
 |
Exact temperature measurement |
|
 |
Positioning |
|
 |
Remote diagnostics |
|
 |
Ethernet/Internet communications |
|
 |
SIWAREX MS weighing module |
 |
HMI functions |
 |
STEP 7-Micro/WIN software with Micro/WIN add-on instruction library |
 |
Compelling systems engineering – now featuring precise dimensioning and optimum solutions for a wide range of different requirements for the complete automation task |
STEP 7-Micro/WIN supports even the most complex automation solution with the following user-friendly wizards: |
 |
TD 100C, TD 200, TD 200C, TD 400C |
 |
PID loops |
 |
High-speed counters |
 |
NetRead-NetWrite |
 |
AS-Interface Wizard |
 |
Ethernet/Internet Wizard |
 |
Positioning Wizard |
 |
Positioning Control Panel |
 |
Modem |
 |
Data Logging |
 |
PID Auto-Tune Control Panel |
 |
PTO (pulse outputs) |
 |
Recipe management |
 |
SIWAREX MS |
 |
Modbus RTU |
 |
USS protocol |
|
|
|
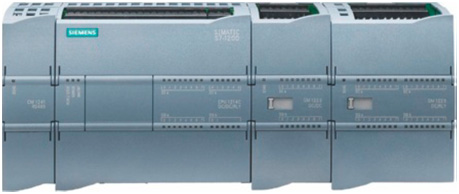 |
 |
The new modular miniature controller from the SIMATIC S7 family |
 |
Comprising: |
|
 |
Controller with integrated PROFINET IO controller interface for communication between SIMATIC controllers, HMI, programming device or other automation components |
|
 |
Communication module with PROFIBUS DP master interface |
|
 |
Communication module PROFIBUS DP slave interface |
|
 |
GPRS module for connection to GSM/GPRS mobile phone networks |
|
 |
Integrated web server with standard and user-specific web pages |
|
 |
Data logging functionality for archiving of data at runtime from the user program |
|
 |
Powerful, integrated technology functions such as counting, measuring, closed-loop control, and motion control |
|
 |
Integrated digital and analog inputs/outputs |
|
 |
Signal boards for direct use in a controller |
|
 |
Signal modules for expansion of controllers by input/output channels |
|
 |
Communication modules for expansion of controllers with additional communications interfaces |
|
 |
Accessories, e.g. power supply, switch module or SIMATIC Memory Card |
 |
The miniature controller that offers maximum automation at minimum cost. |
 |
Extremely simple installation, programming and operation. |
 |
Large-scale integration, space-saving, powerful. |
 |
Suitable for small to medium-size automation engineering applications. |
 |
Can be used both for simple controls and for complex automation tasks. |
 |
All CPUs can be used in stand-alone mode, in networks and within distributed structures. |
 |
Suitable for applications where programmable controllers |
 |
would not have been economically viable in the past. |
 |
With exceptional real-time performance and powerful communication options. |
|
 |
|
|
 |
The modular mini PLC system for the low and mid-performance ranges |
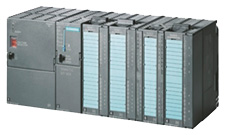 |
 |
With comprehensive range of modules for optimum adaptation to the automation task |
 |
Flexible use through simple implementation of distributed structures and versatile networking |
 |
User-friendly handling and uncomplicated design without a fan |
 |
Can be expanded without problems when the tasks increase |
 |
Powerful thanks to a range of integrated functions |
|
S7-300F |
 |
Failsafe automation system for plants with increased safety requirements for production technology |
 |
Based on S7-300 |
 |
Additional ET 200S and ET 200M distributed I/O stations complete with safety-related modules can be connected |
 |
afety-related communication via PROFIBUS DP with PROFIsafe profile |
 |
tandard modules can be used in addition for non-safetyrelevant applications |
|
SIPLUS S7-300 |
 |
The controller for use in the toughest ambient conditions |
 |
Features an extended temperature range of -40/-25 °C to +60/70 °C |
 |
Suitable for medial exposure (harmful gas atmosphere) |
 |
Condensation and increased mechanical stress is permissible |
 |
Features the proven PLC technology of the S7-300 |
 |
Easy to handle, program, maintain, and service |
 |
Ideal for use in automotive engineering, environmental engineering, mining, chemical plants, material handling, food industry, etc. |
 |
The replacement for expensive custom solutions |
|
|
|
The ET 200S distributed I/O system is a discretely modular, highly flexible DP slave for connection to process signals on a central controller or a field bus. ET 200S supports field bus types PROFIBUS DP and PROFINET IO. ET 200S has protection class IP 20. |
 |
|
Applications : |
You can connect virtually any number of I/O modules in virtually any combination right next to the interface module that transfers the data to the central controller. You can thus set the focus of your configuration on local requirements. Depending on the interface module, each ET 200S can consist of up to 63 modules – for example, power modules, I/O modules, and motor starters. The fact that motor starters can be integrated (switching and protecting any three-phase load up to 7.5 kW) ensures that the ET 200S can be quickly adapted to suit virtually any processrelated use of your machine. The fail-safe modules of the ET200S ensure the fail-safe reading and output of data tosafety category 4 (EN 954-1) |
The ET 200S distributed I/O system is
• Connected to PROFIBUS DP by means of a cable connector for PROFIBUS DP at the IM151-1 or 1M151-1 COMPACT interface module and
• Connected to PROFINET IO at the IM151-3PN interface module by a plug connector for PROFINET IO Every ET 200S peripheral system is
• A DP slave on the PROFIBUS DP or
• An IO device on the PROFINET IO.
• Distributed I/O system to degree of protection IP20 with minimal wiring outlay, also for extremely time-critical tasks such as high-speed closed-loop controls
• Can be used with integrated S7-CPU as mini PLC:
- also available as fail-safe PROFIsafe version
- with optional lower-level PROFIBUS DP
• Discretely-modular design for exact adaptation to the automation task in hand.
• Interface modules available with PROFIBUS DP or PROFINET interfaces
• Can be combined from digital and analog in/output modules, technology modules, motor starters and frequency converters for the control of drives up to 7.5 or 4 kW.
• Exchange of modules during operation (hot swapping), permanent wiring with multi-conductor connection
• Channel-specific diagnostics for high availability
• Can be supplied with integrated fiber optic interface if required
• Transmission rates up to 12 Mbit/s
• FastConnect using unstripped quick connection technology, screw or spring-loaded terminals
• Ex approval to Cat. 3 for Zone 2 acc. to ATEX100 a
• Slot reservation with spare modules
• Fail-safe DI modules with safety-related signal processing according to PROFIsafe
• Option handling – for simplest management of machine options |
|
|
 |
Modular I/O system with degree of protection IP20, particularly suitable for user-specific and complex automation tasks |
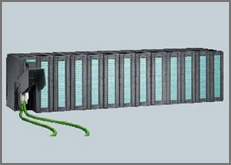 |
 |
Can be expanded with S7-300 automation system signal, communication and function modules |
 |
Applicable Ex analog input or output modules with HART optimize the ET 200M for use in process engineering |
 |
Can be used in redundant systems (S7-400H, S7-400F/FH) |
 |
Consists of a PROFIBUS DP IM 153 connection, up to eight or twelve I/O modules of the S7-300 automation system (assembly with bus connections or active bus modules) and if required a power supply |
 |
Modules can be replaced during operation (hot swapping) with the bus modules active |
 |
Can be supplied with integrated fiber optic interface if required |
 |
Transmission rates up to 12 Mbit/s |
 |
Ex approval to Cat. 3 for Zone 2 acc. to ATEX100 a |
 |
Fail-safe digital in/outputs as well as analog inputs for safetyoriented signal processing in accordance with PROFIsafe |
 |
Support of modules with expanded user data, e.g. HART modules with HART minor variables |
|
|
|
 |
The power PLC for the mid to high-end performance ranges. |
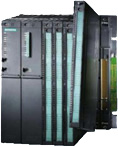 |
 |
The solution for even the most demanding tasks. |
 |
With a comprehensive range of modules and performancegraded CPUs for optimal adaptation to the automation task. |
 |
Flexible in use through simple implementation of distributed structures; user-friendly connections. |
 |
Optimal communication and networking options. |
 |
User-friendly handling and uncomplicated design without a fan. |
 |
Can be expanded without problems when the tasks increase. |
 |
Multicomputing: Simultaneous operation of several CPUs in one S7-400 central controller. Multicomputing distributes the overall performance power of an S7-400. For example, complex tasks can be divided into technologies such as open-loop control, computing or communication, and assigned to different CPUs. And every CPU can be assigned its own local I/O. |
 |
Modularity: The powerful backplane bus of the S7-400 and the communication interfaces that can be connected direct to the CPU enable high-performance operation of a host of communication lines. This enables, for example, division into one communication path for HMI and programming tasks, one for high-performance and equidistant motion control components, and one for a "normal" I/O fieldbus. Additionally required connections to MES/ERP systems or the Internet can also be implemented. |
 |
Engineering and diagnostics: The S7-400 is configured and programmed extremely efficiently together with the SIMATIC Engineering Tools particularly in the case of extensive automation solutions with a high engineering component. For this purpose, high-level languages such as SCL and graphical engineering tools for sequential controls, state graph programs and technology-oriented diagrams are available, for example. |
|
S7-400H |
 |
Fault-tolerant automation system with redundant design. |
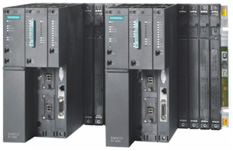 |
 |
For applications with high fail-safety requirements. Processes with high restart costs, expensive downtimes, little supervision, and few maintenance options. |
 |
Redundant central functions. |
 |
Increases availability of I/O: switched I/O configuration. |
 |
Also possible to use I/Os with standard availability: singlesided configuration. |
 |
Hot stand-by: automatic reaction-free switching to the standby unit in the event of a fault. |
 |
Configuration with two separate or one divided central rack. |
 |
Connection of switched I/O via redundant PROFIBUS DP |
|
S7-400F/FH |
 |
Failsafe automation system for plants with increased safety requirements |
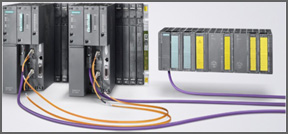 |
 |
Complies with safety requirements to SIL 3 in accordance with IEC 61508, AK6 in accordance with DIN V 19250 and Cat. 4 in accordance with EN 954-1 |
 |
If required, also fault tolerant through redundant design |
 |
Without additional wiring of the safety-related I/O: |
 |
Safety-relevant communication via PROFIBUS DP with PROFIsafe profile |
 |
Based on S7-400H and ET 200M with fail-safe modules |
 |
Standard modules for non-safety-related applications can also be used in the automation system |
 |
Isolation module for joint use of fail-safe and standard modules in safety mode in one ET 200M |
|
|
|
 |
|
|
|
|